Bend Die
The Bend Die is a tool which allows tubes to be bent around it and defines the resulting shape of the bent tubes.The choice of Bend Die depends on the parameters of the bent tube (OD, CLR, DBB, DOB) and on the bending machine. These parameters have a major impact on the size and shape of the bend die.
The size of the groove will depend upon the outside diameter (OD), the center line radius (CLR) and the maximum degree of bend (DOB).
The bend dies are most commonly bolted down. It is also possible to fix it directly to the machine using flanges. The die is usually fixed using a key.
Different types of Bend Die include: Spool, One Piece, Partial Platform, Full Platform, Flange, Horseshoe, Wagon Wheel.
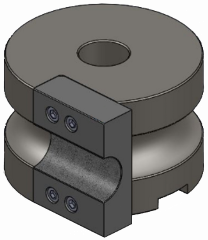
Spool
Spool Dies are full circle dies with a removable grip. They are a cost effective option for bending, and one of the most common types of bend dies that are used.
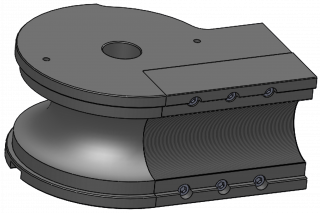
One Piece
One Piece Bend Dies are solid dies with a non-removable grip. Similar to the Spool Bend Die mentioned above, One Piece Bend Dies are also incredibly common throughout the industry.
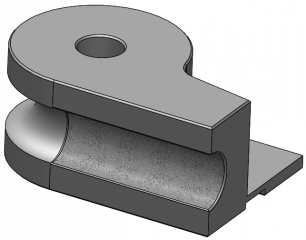
Partial Platform
Platform Bend Dies require additional material around the bend die itself to support it on the machine. A Partial Platform only has additional support on one side of the bend die.
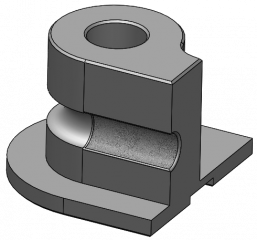
Full Platform
Platform Bend Dies require additional material around the bend die itself to support it on the machine. A Full Platform has additional support around both sides of the bend die.
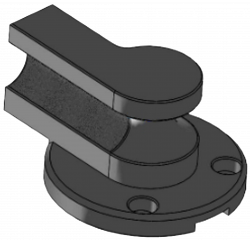
Flange
Flange style dies mount directly to the bend head using bolts instead of having a toolpost and nut. This is useful for very small CLRs where the toolpost will not fit through. Flange dies can be made with spool, one piece or horseshoe dies on top.
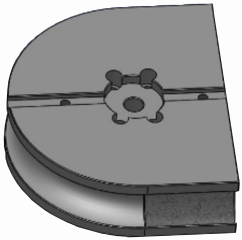
Horseshoe
Horseshoe bend dies are exactly as they sound – they are U-shaped die. Horseshoes can be inserted or one piece. They also have the ability to be a double grip die, depending on the application. Double grip dies provide additional value because they can extend life of the die and allow for grips on both sides.
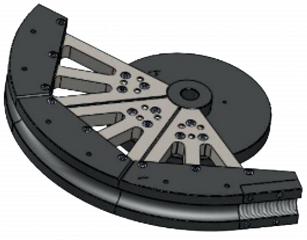
Wagon Wheel
Wagon wheel dies are used whem the CLR of a die becomes very large, typically greater than 20". This style of die is used to save money and weight.
Gripping section
The gripping section grips the tube during the bend. It is often made separately and attached to the bend die. The grip length of the bend die is dependent on the parameters of the tube and usually has a special surface treatment.
The surface of the clamp has a significant impact on the functionality of the tools. There are five basic surface types.
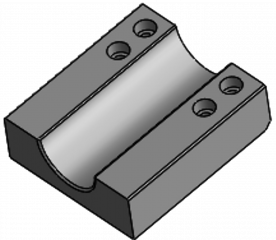
Smooth surface
The least useful, but sometimes necessary, is a groove with no surface treatment. This variant is used in applications where it is necessary to take care of the visual quality of the surface of tube. The disadvantage of this surface is that it requires the use of long clamps so that there are no markings on the pipe from gripping. This option is utilized in the furniture fabrication industry.
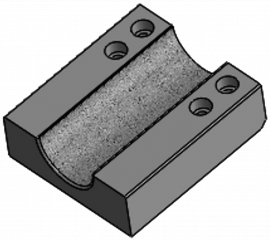
Grit blasted
This treatment is a gentle roughing of the functional surface of the clamp. Compared to the smooth surface, this method does not particularly affect the length of the clamps. Although we do not need to extend the clamps, we cannot shorten them either. The advantage of grit blasted clamps are that they do not lower the quality of the outer surface of the tubes after gripping.
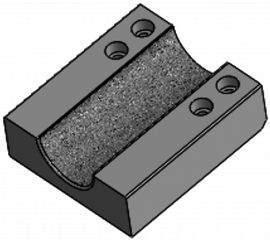
SurfAlloy™
Another way we can treat the surface of the groove is with a carbide-based electric arc spray. This allows us to achieve a greater roughness and also reduce the diameter of the clamp by 0.1mm to 0.2 mm. That's why we recommend producing the diameter of the groove at the nominal diameter of the tube. This has a positive effect on the gripping surface and allows us to shorten the length of the clamp.
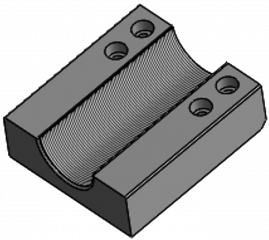
Serration
This surface treatment is a machined serrated surface of the groove. The main advantage of serration is that it allows us to significantly reduce the clamp length. The coarseness of the serration is chosen for the diameter of the tube. It is set by the number of teeth per inch. Typically we would have 12, 16, 20 or 25 teeth per inch.
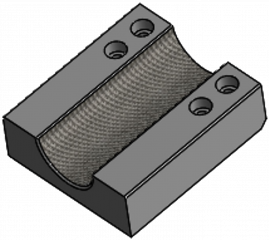
Knurling
This treatment is typically very course. It does leave small marks on the pipe, but it also allows for the clamp length to be significantly reduced. We have three levels of coarseness: 12, 16 or 20-teeth per inch. The coarseness levels depend on the diameter of the tubes, from 30mm to 140 mm. The disadvantage of this solution is that it can only be used for straight clamps, or on straight parts with shaped clamps using insert.