Bend Die
The Bend Die is the tool which the tube is bent around and defines the shape and size of the bend.The choice of Bend Die depends on the parameters of the tube (OD, CLR, DBB, DOB) as well as the features of the bending machine (CLH, Tool post Size, Mounting, Turn Direction). Those parameters have a major impact on the size, shape, and manufacturability of the Bend Die. For instance, the size of the tube groove will depend on the tube’s outside diameter (OD), center line radius of the bend (CLR), and max degree of bend (DOB), and the overall size of the bend die will depend on machine features like stack height and mounting sizes and features. The most common Bend Dies are mounted to a centering tool post, aligned by a key, and tightened down by a nut, but some can be bolted directly to the bender using a flange. The locations of the grip and alignment key are determined by the machine mountings and direction of rotation of the machine.
Different types of Bend Dies include Spool, One Piece, Partial Platform, Flange, Horseshoe, Wagon Wheel, and within those types you may have different inserts, grip selections, and other features.
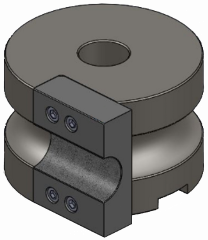
Spool
Spool Dies are full circle dies with a removable grip. They are a cost-effective option and one of the most common types of bend dies that are used.
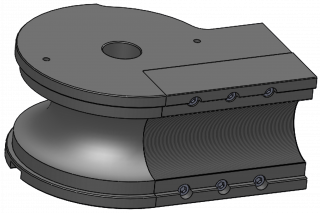
One Piece
One Piece Dies are the most common bend die in the industry. They can come with a removable or non-removable grip and work the same way as Spool Dies with more grip support when longer grip lengths are needed or inserts are not possible.
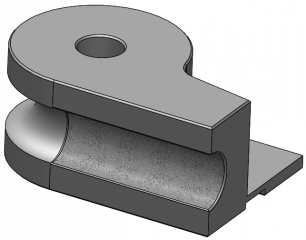
Partial Platform
Platform Bend Dies are used when the die needs additional material for support when bending. Usually in cases where the die is very small. A Partial Platform only has additional support on one side of the bend die.
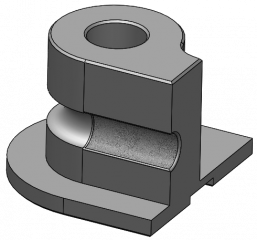
Full Platform
Platform Bend Dies are used when the die needs additional material for support when bending. Usually in cases where the die is very small. A Full Platform has additional support on both sides of the bend die.
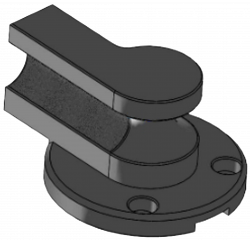
Flange
Flange style dies mount directly to the bend head using bolts instead of a tool post. This is useful for smaller CLRs where the tool post diameter is too large. Flange dies can be made with spool, one piece, or horseshoe dies on top and can be multiple stacks high or even incorporate a built-in tool post on top to mount other dies to.
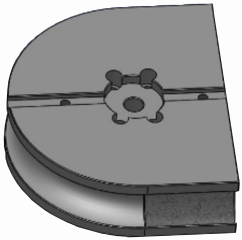
Horseshoe
Horseshoe bend dies are exactly as they sound – they are U-Shaped dies. Horseshoes can be inserted or one piece. They also have the ability to be gripped on both sides to extend the life of the die and possibly allow two direction bending under 180 degrees.
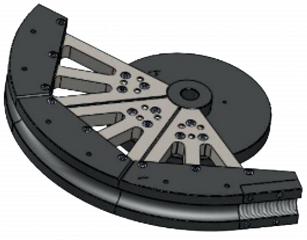
Wagon Wheel
Wagon wheel dies are used when the CLR of a die becomes very large, typically greater than 20". This style makes manufacturing more practical by saving money and weight.
Roller Dies
Some rotary draw bending machines have the capability to use roll or push bending to create larger radius bends. This setup replaces the bend, clamp, and pressure dies with a series of round rollers that bend the tube to an angle and then push it through the rollers to create a more gradual bend.
Gripping section
The grip section grips the tube during bending. It can be made separately and attached to the bend die or made as part of the die. The grip length is dependent on the parameters of the tube and bend and the surface treatment selected.
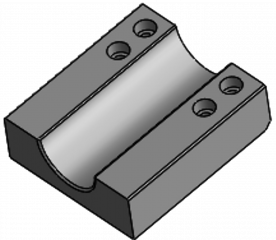
Smooth surface
A smooth grip finish provides the least amount of grip but may be necessary. It is a smooth groove with no surface treatment typically used marking on the tube surface needs to be kept to a minimum. The drawback of this finish is that the grips need to be longer in order to provide enough grip for bending.
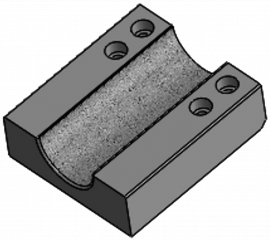
Grit blasted
This is the standard grip treatment for Omni-X. Grit Blast provides more grip than a smooth grip and thus a slightly shorter grip length is needed, while still creating little to no marking on the tube during bending.
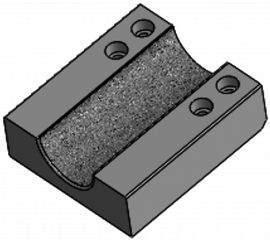
SurfAlloy™
SurfAlloy is a carbide-based electric arc spray that can be applied to the grip section of the bend die. It achieves greater roughness than Grit Blast and reduces the groove diameter by roughly 0.1mm - 0.2mm. This achieves better grip but also can mark the tube more, and we recommend producing the tube groove to the nominal diameter of the tube if this option is chosen to prevent crushing.
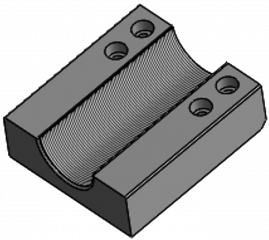
Serration
Serrations are physically machined ridges into the surface of the groove. The advantage of serrations is that they allow us to significantly reduce the length of the grip sections, with the drawback being that they will most likely leave marks in the tube after bending. The coarseness of the serration is chosen by teeth per inch. Omni-X usually used 16 or 32 teeth per inch and can serrate down to tube inner diameters of 5/8".
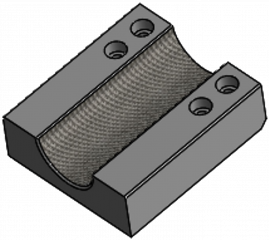
Knurling
This is the coarsest treatment offered. It leaves the most marking on tubes but also allows for the shortest grip lengths. The coarseness is determined by the tube diameter and can be applied to round tubes with diameters as small as 1".
Compound Grips
Compound grips are used when the distance between bends (DBB) is shorter than the grip length of the bend die. Instead of gripping straight tube, the compound is able to grip the previous bend in the tube along with the adjacent straight in order to provide enough grip area to make the bend. Different grip finishes may be used to help with the size of these inserts.